How you like me now?
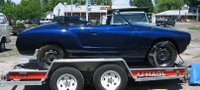
Ok, the strip down was completed - all the wiring, door hardward, dropped the engine and trans, everything out of the front boot. Nothing but car, and wheel.
Next it was off to painting. Off it went to Don Miller's shop in Hamilton, Ohio for prep and paint. Don is an ex-VW shop mechanic, and avid old car buff. He's done a quite a few aircooled Beetles and some Ghias, but he's also old school American Metal - 50's and 60's stuff - he likes the classics.
My choice of color - a late model VW color - Pearlescent Blue Metallic. I fell in love with this color when I saw it on recent Jetta's and Passat's and the pictures here don't quite do it justice. With a camel top and tan interior, this car should be just what I envisioned.
The car went to Don in the spring of 2004. My plan (not Don's) was to have the car done in the fall, so that I could move it back to my garage for final assembly. My work assignment took me out of town, so I wasn't around (once again) to monitor progress - and, as these things go, money was a factor. Don initially suggested media blasting the car, but his was after we'd negotiated price, but before he'd had a chance to really inspect the car - bad move on my part. Shuttling the car out to his shop just to get an estimate wasn't practical. Had I to do it over I would have done so - the cost of a rollback tow truck would not have been prohibitive. It wasn't to be. I should have followed Don's advice, but that would have meant an additional &800, and money was tight. So all of Don's prep work - which is quality work - was done by hand, involving removal of old paint, etc. We still came away with a quality job but next project will plan for media blasting if for no other reason that to ensure complete removal of paint, bondo, rust, and grime.
Don did make sure to paint the front boot and the engine compartment, along with the areas behind the rear seat and the door jambs - a complete job. For these ancillary areas, manual paint removal must have been a pain, but it was done and would have been much easier by media blasting.
These pics show the car trailered up and off to my new home - in May of 2005.